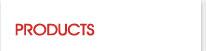
Add: 15th Fl. 691, Renmin Road North, Guangzhou, China
Tel: +86-20-81074430, 81068419
Fax: +86-20-81084009, 81072170
Email: dyechem@gzchem.com

APPLICATION OF VAT DYES
Aims:
1. To apply a vat dye dispersion to a fabric by padding
2. To apply a vat dye to cotton fabric using a pre-pigmentation method
3. To observe the changes a vat dye undergoes during application to a fabric
4. To determine the effect of soaping on a vat dye
5. To practice pad-bath calculations.
Theory:
The simplest arrangement for dyeing fabric is to pull the textile material through the
dyebath so that the dye can exhaust on to the fabric surface. Low liquor ratios and the
addition of common salt or Glauber's salt both promote such exhaustion. In some cases,
the addition of acid also promotes exhaustion. If the dye is only partially soluble in water
and likely to be exhausted unevenly, the addition of soap or sodium carbonate may
promote leveling. A dyeing is considered to be level if all parts of all fibers have been
penetrated evenly and completely. Machines for this type of dyeing are called batch
machines.
• Package and beam machines for yarns.
• Jigs for open width fabrics
• Winches for woven and knitted fabrics in rope form
• Jet dyeing machines for knitted fabrics in rope form.
• Paddle machines for sewn products like bedspreads
• Smith drums for nylon hosiery or special machines for nylon hosiery
If a dye is not soluble in water, as is the case with vats, it may be applied to the fabric as a
dispersion by a padder. Once the insoluble vat dye has been uniformly applied to the
fabric surface, usually with the aid of special dispersing agents (detergents), it can be
solubilized by reaction with a reducing agent, e.g., sodium hydrosulfite ("hydros",
Na2S2O4) in dilute NaOH. Once it has been converted to its soluble (LEUCO) form, the
vat dye can penetrate into the cotton fibers. After adequate time for penetration to occur,
the fabric is withdrawn from the bath and oxidized by air or an oxidizing agent such as
sodium perborate or hydrogen peroxide. This process is schematically represented below.
pad hydros
vat dye (insol) → on fabric surface → LEUCO form (soluble)
NaOH
air oxidation
vat dye
(insolublized inside. fibers)
Before chemical reducing agents were readily available, vat dyes were converted to their
soluble leuco form by fermentation of organic matter in wood tubs called vats. This
method of reduction and application is the source of the name for this class of dyes.
2
Once the vat dyes have been regenerated inside the fiber, they are very insoluble. This
accounts for their excellent wash fastness.
Because they can be applied as a dispersion by padding, solubilized by reduction, and
finally reoxidized when inside the fibers, vats are well- suited to continuous dyeing
operations. Such treatments exhibit a number of advantages:
a) very efficient use of the dye. All that is made up can be applied.
b) the insoluble vat is very evenly distributed over the fabric surface, leading
to level dyeings
c) continuous processes are normally more economical processes than batch
processes
Equipment and Chemicals
Bleached 100% cotton (8" x 24")
C. I. Vat Green 1 (20 g/L) Indanthrene Green FFG
Dispersing agent (10 g/L)
Alginate NVS (sodium alginate, 1 g/L)
Soap solution (50 g/L)
NaOH solution (100 g/L)
Sodium hydrosulfite (hydros) (100 g/L) ..
Sodium chloride solution (100 g/L)
The diagram below illustrates how your fabric is to be labeled and cut for testing.
20cm
20cm 20cm 20cm
Padded &Dried Padded, Reduced, Padded, Reduced,
Oxidized & Dried Oxidized, Dried & Soaped
PD PROD PRODS
3
CAUTION -WEAR SAFETY GLASSES AT ALL TIMES DURING THIS DYEING!
Experimental Procedure:
1. Cut an 8 x 24" piece of cotton fabric from the roll and weigh it to two decimal
places in the balance room.
2. Familiarize yourself with the operation of the laboratory padder. You should
know
(a) how to adjust the pressure on the "nip" rolls
(b) how to safely start and stop the rolls
(c) how to pass ("dip") a swatch of fabric through the pad bath so that it is
saturated and then squeezed between the rolls
3. The following pad bath has been prepared for you and placed in the trough of the
padder:
• 20 g/l C.I. Vat Green 1
• 10 g/l Dispersing agent.
• g/l Alginate NVS (8%solution)
• water to a final volume of 500 ml.
4. Obtain one pair of disposable gloves for each person. Be certain that the padder is
adjusted to 25lbs. Save your gloves for use later.
5. Start the rollers and turn on the air pressure to close the nip. The nip should never
be closed under pressure while the padder is not running, as this will cause a flat
spot on the rollers and result in uneven application of chemicals to the fabric.
Feed the fabric into the nip of the padding mangle. Allow the fabric to pass
through the dye dispersion and collect the fabric from the bottom of nip.
BE CAREFUL WHEN PICKING UP THE FABRIC AS IT EXITS THE
MANGLE NIP UNDERNEATH THE PADDER.
6. Pass the fabric through the padder twice to ensure even application of the colour.
7. Quickly weigh the padded fabric so that its % Wet Pick Up may be calculated. Be
certain that the balance pan is protected from the wet fabric by placing a large
watch glass on the balance pan
8. Cut the 8 x 8" PD (padded and dried) swatch from the fabric and dry it in the
oven. From it you will cut two 2 x 2" squares for your reports and a 3 x 6"
diagonal swatch for Rub fastness testing.
4
9. Multiply the original weight of your fabric by 0.67 (you have just cut 113 of it
off) to obtain the amount of fabric that will be placed in the hydros reduction bath.
The following is the ratio of chemicals that is necessary for EACH 10.0 g of
fabric. Liquor ratio is 30:1. You will need to calculate how much of each
ingredient you will need for your bath.
• 15 mL of 10% (wt/vol.) caustic soda
• 10 mL of 10%sodium hydrosulfite (Na2S2O4.)
• 10 mL of 10% sodium chloride
• 275 mL of water
Be certain to adjust all chemicals AND water to the weight of your sample.
CAUTION!!! DO NOT GET THIS BATH ON YOUR SKIN!!! USE GLOVES!!!
10. Place the beaker in the WATER BATH and heat to 70 -80°C (160 - 176°F).
Gently stir the bath to be certain that the hydro is mixed well.
11. Immerse the padded fabric in the warm hydro reduction bath. Occasionally turn
the fabric with a stirring rod to insure uniform reduction of the vat dye. To avoid
premature oxidation of the leuco form of the dye, keep the fabric beneath the
surface of the bath, if necessary weight the fabric. Note any changes in the
appearance or color of the fabric during this "vatting". Leave the fabric in the bath
for 20 minutes so that the dye can be reduced and then penetrate into the cotton
fibers. .
12. Remove the fabric from the bath; squeeze out excess reduction bath, and hang the
swatch over your sink till the original green color is regenerated (5-10 minutes).
13. Cut this sample in two equal pieces. Dry the Padded, Reduced, Oxidised & Dried
PROD sample and cut it as you did the PD sample.
14. Prepare a scouring bath by mixing 32 ml of 5% (wt./vol.) stock soap solution with
enough water to make 800 ml of solution. Place this soap solution and the PRODS
sample in a stainless steel beaker. Heat this solution at or near the boil on a hot
plate for 10 minutes. Remove the sample, rinse it well with water, and dry it. This
soaping removes loose surface dye particles and causes some aggregation of
particles inside the fibres. The latter change improves the wash fastness of the
dye.
15. Cut PRODS as you did the other two samples. You should now have three strips
(3 x 6") for evaluation of crocking fastness.
16. Record any differences in the appearance of the three fabric strips.
17. Test all three samples for colorfastness to crocking by AATCC Test Method 8.
Evaluate the results of the crocking test with the Grey Scales. Information about
and directions for this test is attached.
5
Purpose of the test:
To determine the degree of color that may be transferred from the surface of a colored
textile material to other surfaces by rubbing.
Principle:
A colored test specimen is fastened to the base of the Crockmeter and rubbed with a
white crockfastness test square. The Crockmeter simulates the rubbing action of a human
finger and forearm. The amount of color transferred by rubbing is assessed with the Grey
scales.
Procedure:
1. Cut a test specimen at least 3 x 6", preferably with the long dimension diagonal to
warp and weft directions. .
2. Place the test specimen on the base of the Crockmeter so that it rests flat on the
brasive cloth with the long dimension in the direction of the rubbing action.
Fasten the sample with a stain- less steel sample holder or a piece of masking
tape, placed so that it won't interfere with the rubbing action.
3. Mount a 2 x 2. square of bleached cotton fabric (crockmeter square), with the
weave oblique to the direction of rubbing, over the end of the finger that projects
downward form the weighted sliding arm. Use the special wire pinch clamp to
hold the square on the finger.
4. Lower the covered finger onto the test specimen and cause it to slide back and
forth twenty (20) times by making TEN COMPLETE TURNS of the crank
CLOCKWISE at a rate of one turn per second.
5. Remove the white test square and evaluate the amount of color transferred from
the specimen to the white square by means of the Grey scales.
References
1. Baumgarte, U. and Schluter, H. Continuous Dyeing with Vat Dyes, Textile
Chemist and Colorist, 11(1), 27 (1985).
2. Giles, C. H., A Laboratory Course in Dyeing, 2nd Ed., 1971.
1. Trotman, E. R., Dyeing and Chemical Technology of Textile Fibers, fourth
edition, 1970.
2. Arthur D. Broadbent, The Basic Principles of Textile Coloration. Society of
Dyers & Colourists, 2001
